ULTRASONIC LEVEL SENSOR – what is it?
The ultrasonic level sensors consist of two essential parts, a transducer (also called sensor) and an electronic control box. The transducer cannot work alone without the control box. The control box can be conveniently placed in a control room or some other location and connected to the transducers via coaxial cables. The transducers are mounted at the top of the tanks, pointing downward to the liquid’s surface.
A strong ultrasonic signal burst is then generated by the transducer and propagates through the air down to the liquid’s surface. The ultrasonic signal will not penetrate below the surface of the liquid, it will be reflected back to the transducer. The echo round trip time is then converted to level, which is defined as the actual depth of the liquid in the tank. It is important to mention that the measurement is not affected by specific gravity, viscosity or any other characteristic of the liquid being monitored.
Typical Ultrasonic Level Sensor for a single tank:
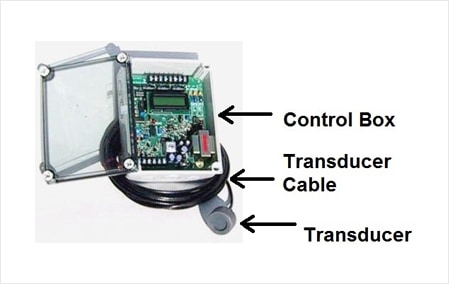
DISADVANTAGES of Ultrasonic Level Sensors are few:
- The only significant issue presents itself when the liquid produces a thick foam on the surface. This foam will absorb the signal. In such cases, if the foam cannot be removed, the ultrasonic level sensors should not be used. Fortunately, this rarely occurs.
- For the best accuracy and proper monitoring, the transducer requires a clear and unobstructed view of the surface it monitors, free of obstructions directly under it.
Please see also Ultrasonic Level Sensor Overview
ADVANTAGES of Ultrasonic Level Sensors are many:
- There are no moving parts, nothing to wear out.
- There is no maintenance, nothing to clean or lubricate. No gaskets or seals to replace.
- There is no calibration, once the ultrasonic level sensor is installed properly, it will keep on working for some 20+ years (depending on quality of installation), requiring no attention.
- Transducers are not affected by vapor condensation, or fumes inside the tank. In the past there used to be claims that fumes absorb ultrasonic signal. That is a myth. The problem was caused by insufficient product quality or an improper installation. Measurement is not affected by liquid density, specific gravity, viscosity, etc.
- Transducers are available in variety of housings to suit the corrosive environments in tanks, typically PVC, Teflon, stainless steel and explosion-proof for hazardous, flammable liquids. We have had a case where a barge transportation firm requested that our stainless steel transducers were plated with 24 karat gold, to offer best corrosion resistance for the fluids they transport.
- Transducers are hermetically sealed, waterproof, splashing of liquids or immersing in liquid will not cause damage.
- Ultrasonic level sensors allow multiplexing, where several tanks can be monitored by one control box. This results in significant cost reduction. Another significant advantage and cost saving of multiplexing is that all transducer cables can be placed in the same conduit. Automated Sonix Corporation has two models of this kind. Sonix-1000 can monitor up to seven (7) tanks, UC-4000 monitors up to nine (9). Both control boxes can be placed several hundred feet from the monitored tanks. Level and volume of each monitored tank are shown on one control panel in sequence. Both models have a computer connectable output to save the data in your computer. The protocol is RS232C, uses only 2 wires and can transmit up to 2000 feet distance.
Automated Sonix Corp.
Go to Ultrasonic Level Sensor Overview
We encourage you to call us or send email about your
application. Tel: 941-964-1361